Mölnlycke Procedure Trays efficiency study
By implementing surgical procedure trays, European hospitals achieved 40-55% time savings in the operating room, making it possible to carry out more surgical procedures – around 37% more procedures in one hospital in France.
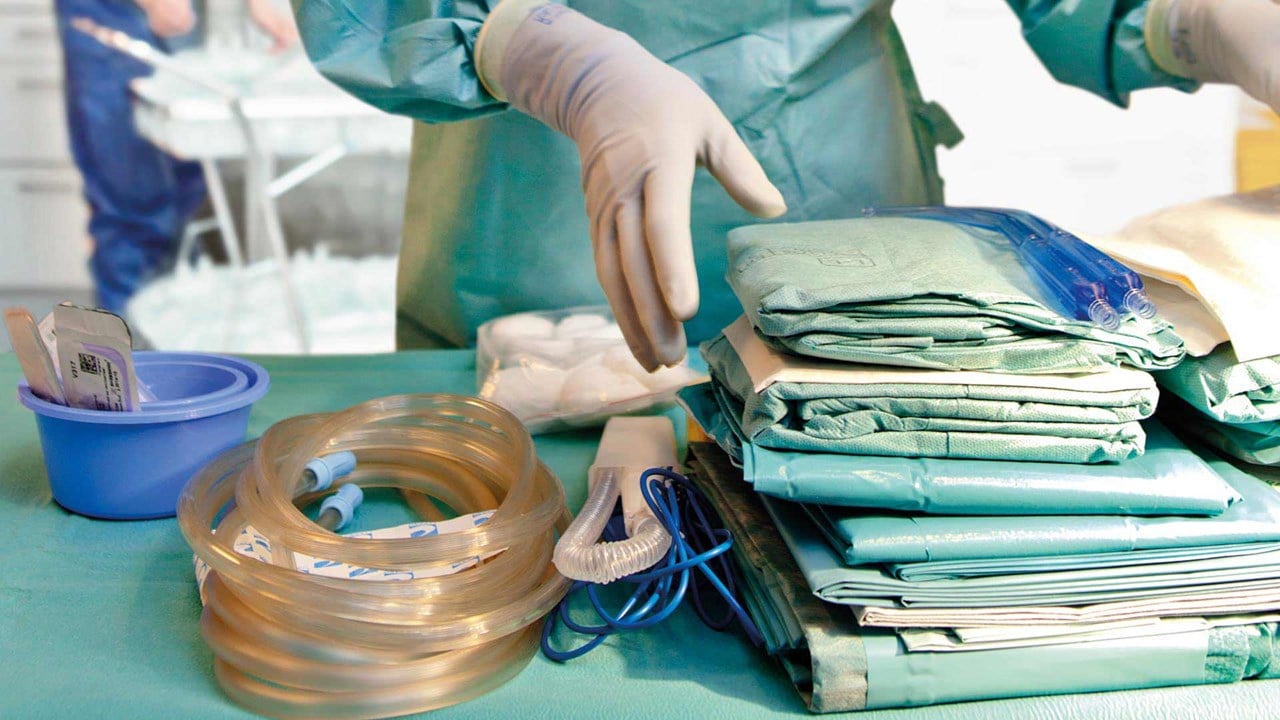
Introduction
Hospitals in Europe are traditionally supplied with single-packed sterile products for surgical procedures. For each procedure, the nurses in the operating room need to collect required materials from the storeroom unit by unit and set it all up for each procedure. Other necessary steps to get the right material in place include stock-taking and ordering, as well as warehousing and transportation.
Hospital management today is striving for the most efficient treatment procedures without compromising on quality or safety. Thus there is increasing pressure to handle more interventions while relying on unchanged resources
Aim
The aim of the study was to investigate the effects and quantify the time-savings when implementing Mölnlycke Procedure Trays.
This was an open prospective study performed as case studies in different hospitals located in Germany, France and Sweden. A total of 26 different Mölnlycke Procedure trays were used. For each of the hospitals the single-use material process was studied, from ordering of materials to disposal. This process typically consists of 6 main processes: internal order and delivery, receiving of goods in the surgical department, preparation and clean up of surgery, external order, receiving of goods via the purchasing department and invoicing
The steps can be broken down into sub-processes and activities. For example, the main process – preparation and clean up of surgery – can be broken down into 14 sub-processes or 33 activities. Each step in the process was described and measured both before and after implementation of the Mölnlycke Procedure trays. For every step of the process, the time and cost drivers were identified by studying practical use and measuring time.
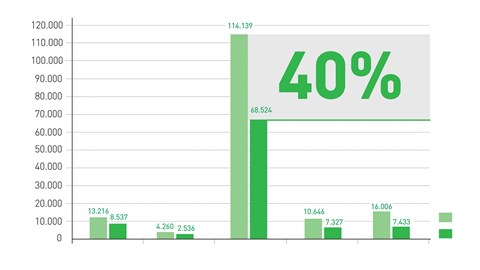
The results of the study show that following the introduction of Mölnlycke Procedure trays, time-savings in the single-use material process were between 40% and 59% in the hospitals studied.
Table 1: Summary of time-savings
Hospital | Number of Mölnlycke Procedure trays used | Annual number of surgeries | Total time saving (hours) | Total time-saving (%) | Time saving in prep. and clean up (%) |
France | 3 | 4199 | 2699 | 59 | 55 |
Sweden | 12 | 3005 | 2047 | 59 | 48 |
Germany | 11 | 2785 | 1060 | 40 | 40 |
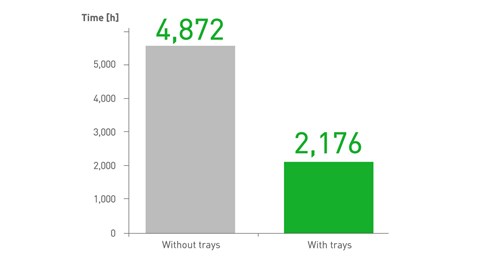
The magnitude of the time-savings depends on several factors,including the number of different Mölnlycke Procedure trays used, number of components in each tray and the number of procedures performed with trays. The largest time-savings were found in the preparation and clean up of surgery, but time-savings were also shown in other process steps.
The time-savings were used in different ways depending on individual objectives of the hospital, for example:
- Performance of additional surgical procedures, giving patients more timely treatment.
- In the French hospital 37% more surgical procedures were performed following implementation.
- In the German hospital the number of interventions increased by 18% per year.
- Training of staff.
The results of the case studies show that significant time-savings(40-55%) can be gained through implementing Mölnlycke custom procedure trays for surgical procedures in the operating room. The freed up time makes it possible to perform additional surgical procedures. The financial effect of this is an area for further research.
'References'